Important Factors To Consider for Troubleshooting and Repairing Your Product Packaging Equipment
When attending to the intricacies of troubleshooting and repairing your packaging maker, numerous vital factors need to be taken into consideration to ensure both effectiveness and safety. From comprehending usual mechanical and electrical problems to using appropriate analysis tools, each step plays an essential role in preserving operational honesty. Moreover, adherence to safety procedures and using OEM components can substantially affect efficiency. Lots of neglect the details of routine maintenance and documentation, which are important in avoiding future problems. What various other important aspects could be the key to boosting your machine's integrity?
Recognizing Usual Concerns
Determining common problems in packaging makers is essential for keeping operational efficiency and lessening downtime. Product packaging makers, important to assembly line, can run into a selection of troubles that hinder their efficiency. One widespread concern is mechanical breakdown, usually arising from damage on elements such as belts and equipments, which can lead to inconsistent packaging high quality.
One more common problem is imbalance, where the packaging materials might not straighten correctly, creating jams or incorrect securing. This imbalance can stem from improper arrangement or changes in material requirements. Furthermore, electric failures, such as damaged sensors or control systems, can disrupt the device's automated processes, causing manufacturing delays.
Operators may likewise experience obstacles with software application problems, which can influence maker programming and performance. In addition, inadequate maintenance practices usually add to these issues, highlighting the demand for normal inspections and prompt solution interventions. By comprehending these typical concerns, drivers can apply aggressive actions to ensure peak performance, consequently decreasing expensive downtimes and boosting overall productivity in product packaging procedures.
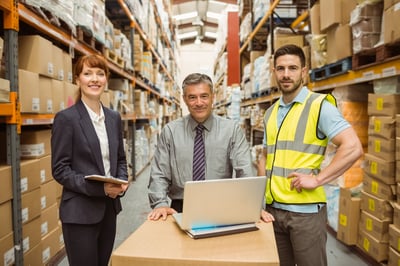
Analysis Tools and Methods
Efficient troubleshooting of packaging makers relies heavily on a selection of analysis devices and methods that promote the recognition of underlying problems - packaging machine repair service. Among the key devices is the use of software application diagnostic programs, which can check device efficiency, evaluate mistake codes, and offer real-time information analytics. These programs enable service technicians to pinpoint certain breakdowns rapidly, dramatically decreasing downtime
Along with software program options, oscilloscopes and multimeters are vital for electric diagnostics. Multimeters can gauge voltage, existing, and resistance, aiding to recognize electric mistakes in circuits. Oscilloscopes, on the other hand, offer visualization of electrical signals, making it much easier to identify abnormalities in waveforms.
Mechanical issues can be identified using vibration analysis tools and thermal imaging cams. Resonance evaluation enables the discovery of discrepancies or misalignments in equipment, while thermal imaging assists identify overheating components that might result in mechanical failure.
Last but not least, aesthetic inspections, incorporated with common lists, continue to be invaluable for basic troubleshooting. This comprehensive method to diagnostics guarantees that service technicians can successfully attend to a vast array of problems, thus enhancing the reliability and efficiency of product packaging makers.
Security Protocols to Adhere To
Exactly how can packaging machine drivers make certain a risk-free workplace while fixing? The implementation of rigorous safety and security procedures is necessary. Operators ought to start by separating the maker from its source of power prior to initiating any troubleshooting treatments. Lockout/tagout (LOTO) methods have to be imposed to stop unintentional look at here re-energization throughout maintenance.
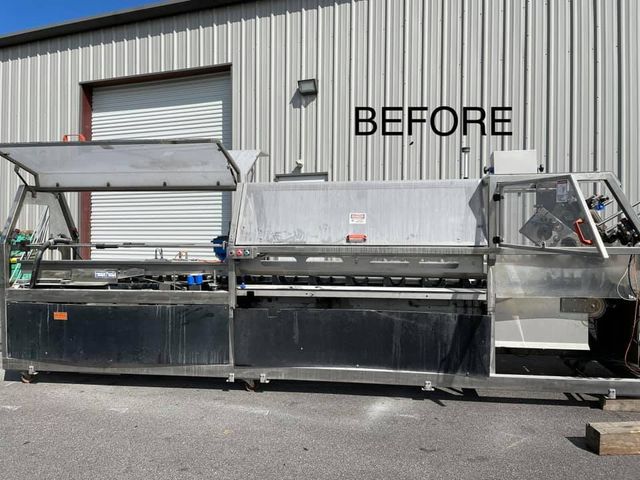
Operators needs to likewise acquaint themselves with the maker's safety and security attributes, such as emergency stop switches and safety and security guards, verifying that they are practical prior to starting any diagnostic work. packaging machine repair service. It is crucial to connect with team members, ensuring all workers recognize the ongoing troubleshooting activities
Last but not least, operators should record all procedures and searchings for, providing a clear document in situation of future issues. By sticking to these safety and security methods, product packaging equipment operators can develop a safer setting, lessening risks while efficiently repairing and repairing equipment.
Components Replacement Standards
When it concerns preserving product packaging devices, recognizing components replacement standards is important for guaranteeing ideal efficiency and longevity. Consistently analyzing wear and tear on machine components is important, as timely replacements can prevent much more considerable damage and costly downtime.
First of all, always refer to the producer's specifications for suggested substitute periods and part compatibility. It is important to make use of OEM (Original Equipment Manufacturer) parts to assure that replacements meet the needed top quality and efficiency criteria.
Before starting any kind of replacement, ensure the machine is powered down and properly secured out to stop accidental activation. Paper the condition of the changed components and the day of substitute, as this will certainly help in monitoring upkeep fads over time.
Furthermore, assess the bordering parts for indications of wear or prospective concerns that may emerge from the replacement. This alternative method can alleviate future problems and improve operational Go Here performance.
Lastly, after replacing any kind of components, conduct thorough screening to ensure that the maker is functioning properly which the new parts are incorporated flawlessly. Following these guidelines will not only extend the life of your packaging maker but likewise boost overall efficiency.
Maintenance Best Practices
Constant maintenance methods are vital for taking full advantage of the efficiency and life expectancy of product packaging devices. Developing a detailed upkeep timetable is the initial step towards making certain ideal efficiency. This schedule needs to include daily, weekly, and month-to-month jobs tailored to the details machine and its operational needs.
Daily checks need to concentrate on crucial elements such as belts, seals, and sensing units, guaranteeing they are clean and working correctly. Weekly maintenance could include examining lubrication levels and tightening up loose installations, while month-to-month jobs ought to include much more comprehensive analyses, such as positioning checks and software program updates.
Utilizing a checklist can simplify these procedures, making sure no essential jobs are overlooked. In addition, preserving precise records of upkeep tasks helps identify persisting concerns and educates future methods.
Educating staff on appropriate use and handling can substantially minimize damage, stopping unnecessary malfunctions. Furthermore, spending in top notch components and lubes can enhance maker efficiency and reliability.

Conclusion
Finally, reliable repairing and repair work of packaging makers require an organized method encompassing security methods, the use of ideal diagnostic tools, and adherence to maintenance best methods. Regular assessments and prompt parts replacement with OEM components play an essential role in maintaining device efficiency and reliability. In addition, careful documentation of treatments and findings contributes to a much deeper understanding of recurring problems, eventually improving operational effectiveness and minimizing the probability of future malfunctions.
When resolving the complexities of troubleshooting and fixing your packaging maker, a number of crucial factors should be taken into consideration to ensure both effectiveness and safety.Determining usual concerns in packaging equipments is important for preserving functional efficiency and reducing downtime.Reliable troubleshooting of packaging equipments relies heavily on a range of diagnostic devices and techniques that help with the recognition of underlying concerns.Just how can packaging maker drivers make certain a secure functioning environment while troubleshooting?In conclusion, efficient troubleshooting and repair service of product packaging machines demand a structured method encompassing safety protocols, the use of ideal analysis tools, and adherence to upkeep ideal methods.